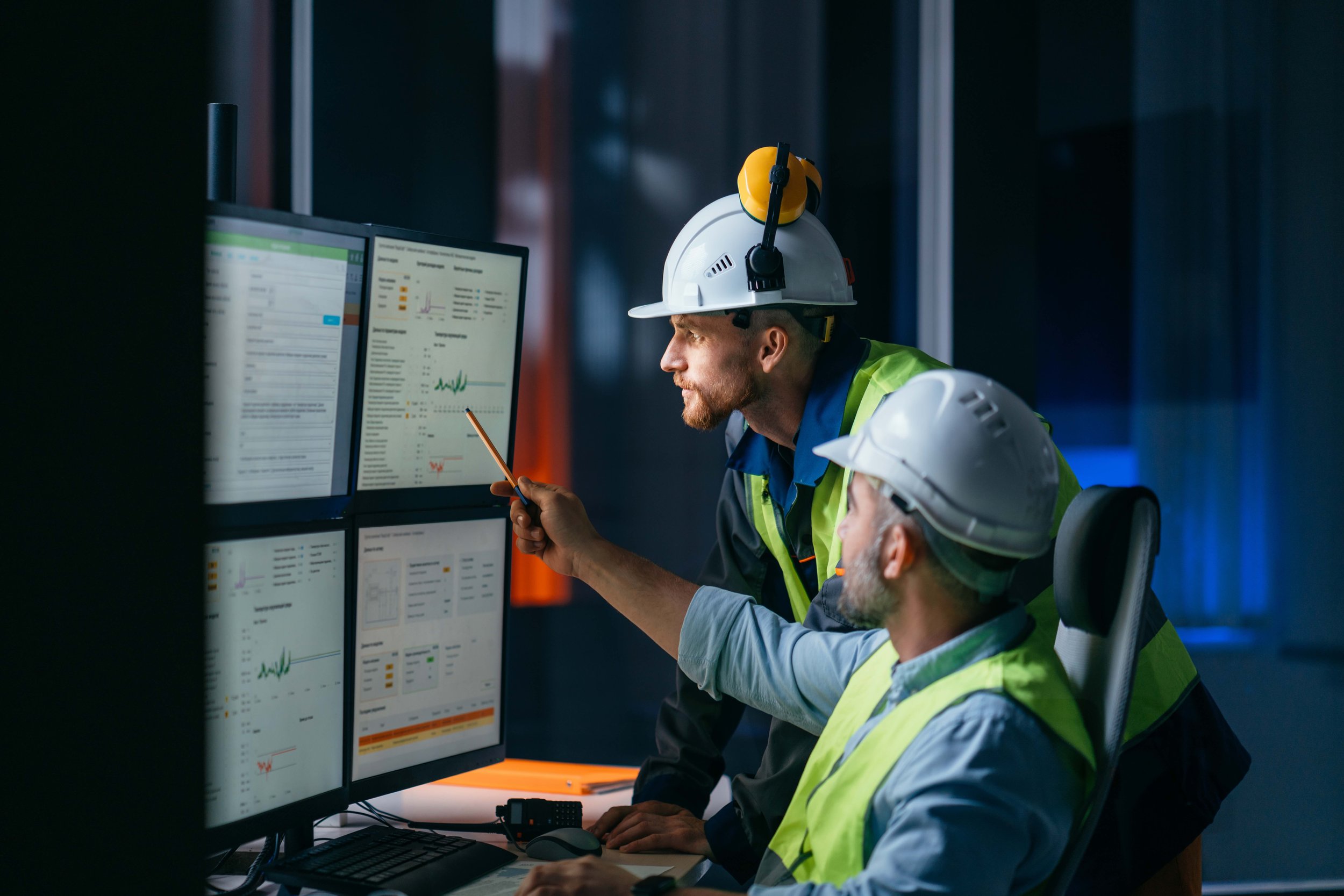
Predictive Industrial Maintenance Strategies
Regular maintenance is required to prevent breakdowns, optimize equipment performance and extend the lifespan of machines and tools. A proactive approach to maintenance ensures the facility operates at peak performance, reduces costly downtime disruptions and increases ROI.
Predictive maintenance strategies to keep your operations running smooth
Many manufacturers are transitioning from preventive maintenance to predictive maintenance tools, unlocking greater efficiency. Traditional time or usage-based maintenance aims to prevent breakdowns but can lead to over-maintenance, under-maintenance, or unnecessary work. Predictive maintenance solutions offer a proactive, data-driven approach that boosts ROI, enhances output, eliminates unplanned downtime, and reduces equipment failures.
Predictive Maintenance
-
Data Driven Decision
By harnessing predictive maintenance tools, we facilitate informed decisions grounded in data-driven intelligence, transcending guesswork and instinct.
-
Preemptive Maintenance
Our predictive maintenance services employ advanced analytics to provide valuable insights, empowering you to anticipate and prevent costly downtime before it occurs.
-
Condition-Conscious Monitoring
We establish baselines for your current operating conditions, then leverage data and analytics to uncover critical trends, enabling timely interventions.
Tempus establishes baselines for your current operating conditions and then employs data acquisition and predictive analytics to uncover critical trends. By providing insights into potential issues within production machinery, technicians can make informed decisions.
Predict the Future with Heat Mapping
Early detection with thermographic testing, or infrared inspection, is a predictive maintenance method that prolongs equipment lifespan. It identifies issues in real-time, empowering manufacturers to take proactive measures, reduce unplanned downtime, optimize repair schedules, and lower maintenance costs.
Keep Lubricants Flowing
Changing lubricants based solely on time or usage can increase downtime and operational costs. Routine fluid analysis lets manufacturers predict when lubricants need replacement while providing insights into the machine's overall health. This predictive maintenance solution helps maximize uptime and efficiency.
Vibration Monitoring
Maintain optimal rotation with Vibration monitoring and analysis to prevent deferred maintenance that can compromise product quality. Our structured vibration analysis program helps manufacturers avoid quality issues and machinery breakdowns, keeping rotating equipment in peak condition.
Cut Waste with Leak Detection
Integrating leak detection into your predictive maintenance approach provides valuable insights into equipment performance. This empowers optimized maintenance schedules, extended machinery lifespan, improved safety protocols, and reduced production losses.